COST REDUCTION IN TECHNOLOGY
FOR GAS TRANSPORTATION AND STORAGE
USING
ECOFILT MIKROFILTERJános
KIRÁLY1, Róbert KOVAC2 and
László LIVO1
1- MARKETINFO, Hungary
2- HELIR, Serbia and Montenegro
Abstract:
aaThis work presents filter installation
suitable for mechanical filtering of natural and other
types of transported gas. Minimal
particle size can be less than 2 microns.
aaDuring the last decade Ecofilt Mikrofilter has proved its
applicability in underground gas storage, gas
transportation and
with other various users. Ecofilt Mikrofilter allows the user to
plan his filtering costs and to ensure maintenance costs
optimization in advance. The plans are feasible and
realistic, which have been proved by the experience of
its current users
in gas industry in Hungary and Serbia and Montenegro.
aaEcofilt Mikrofilter is a filtering
installation with working period of 10 years. Its ability
to perform strict particle filtering
derives from the very technology used for its make. The
filter's guaranteed layer and body are made of stainless
steel, which
gives the filter longevity and hardness (high deltap) and
makes it easy to clean and maintain.
aaThe filters can be installed into any
existing housing. In such cases the filters can take more
flow, the filtering is more
accurate, and the safety is also increased when compared
to the original construction. High permeability also
derives from
the technology. It allows for small initial resistance
(only a few millibars) and gives rather high tolerance to
impurities.
aaThe very possibility to plan ahead allows
the user to select the most suitable filtering
installation, which would also allow
the user to lower the initial investment costs as well as
the maintenance costs.
aaIn summary, the most important fact about
these filtering installations is that they have long
lifetime, require low initial and
low or insignificant maintenance costs, since they lead
to lower instument damage rate by protecting them. This
can be proved
by dramatic cost decrease.
aaThis work presents design,
construction/installation and application of the filters,
as well as the users' experience in use of them.
Key
words: filter, gas, costs, maintenance.
1.
Mechanical filtering - introduction
aaTo introduce mechanical filtering, let us
first see what it is about; an experiment would be a good
starting point. Take a full
glass of drinking water and pour the content to another
glass through filter paper (or through a serviette).
After the filter dried,
we can see that colour of the paper has changed. This
would indicate that the water had contained some elements
- impurities,
which remained on the filter paper. If we repeated
pouring several times, the filter would come to a point
where it could no
longer let the water flow through. Particles that had
kept on the filter formed an impregnable layer. If, on
the other hand, we
analysed the water at lab after each pouring, we would
see that it contained less and less impurities each time.
aaWhat is the explanation of this
phenomenon? On the filter paper surface a filter cake is
formed, which is made of impure
particles that are also part of the filtering process.
This leads to the conclusion shown in Figure 1.
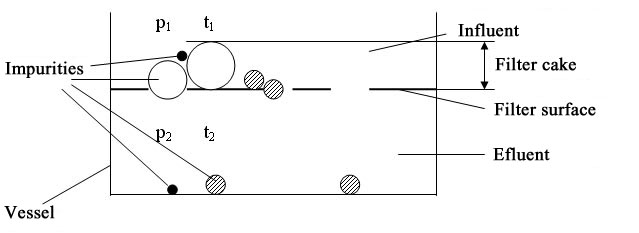
Fig. 1
Mechanical filtering
aaThe experiment results gives us certain
knowledge: impurities can be found in both to be filtered
and has been filtered medium
(influent and efluent, respectively), but in different
contents. Another result is that the filter cake contains
impurities of different
size and shape.
aaIf we repeated the experiment with an
other filter type, for example we used a piece of cloth
instead of filter paper, the results
would also differ, first in time taken to filter the
water. To be more accurate, if the quantity of water was
different, so would be
the time of filtering. That would lead to the difference
in filter cake formed on the cloth. Taking all previous
results into
consideration, we can say that the quality and refinement
of filter are not the only factors that influence the
filtering results. To
keep the process under control we need to consider more
factors.
2.
Filtering characteristics
aaAnalyzing results of the previous
experiment, we can conclude that the most important
characteristic of a filter is its refinement,
which is determined by separation parameter. Its mark is
µm (micrometer = 0.001 mm). Other important parameters
are filtering
surface (or filtering area - square meter - m2)
and free light area (%).The free light area is a number
directly dependent on filter
quality. This number indicates the initial size of the
filter area through which a fluid can flow continually.
aaIt is now easy to conclude that over a
course of time the light area is reduced, owing to
formation of filter cake. On each side
of filter the allowed pressure difference (deltap) is
resenst, which is a significant property to have in mind
in filter manufacturing.
Filter data has great influence on fliter cake, its
thickness and filtering time.
aaApart from the parameters given above,
there are other equally important ones that should be
considered in designing filtering
technology: filter material, filtering fluid, medium
temperature, pH, electric conductivity, etc. Two aspects
allow optimal filtering
results:
aaaaaa) identification of an existing system
operation and possibility of improvement of filtering
technology based on laboratory
aaaaaaaanalyses,
aaaaab) well selected final goal of filtering
process and its results' confirmation in a lab.
3. Main types of mechanical filters
aaMechanical filters can be divided in two
main types. Surface filters are those
with flat surface, e.g. net, sift, or those of
certain geometric shapes, which surface can also be used
as filter (cylinder, cone, dome). These filters are
candle or plate
shaped, and filter cake is formed on the surface (Fig.
1).
aaAnother type is the deep bed
filters, which spread into the third dimension.
The third direction is usually much smaller than
the other two.
aaOperation of the two filter types is
basically different. While the surface filter strictly
separates suspended solids from the
filtered fluid, the deep bed filter's separation can not
described with one dimension, only with thickness
territory.
aaIn deep bed filters, there is no filter
cake formation; any changes are made in the third
direction, and they depend on how and
where certain granules are positioned; the granules then
flow through or are suspended in channels that are formed
during the
filtering process. The channels' dimensions are
influenced by design, material, geometry (diameter) and
permeable layre of the
deep bed filter (Fig. 2).
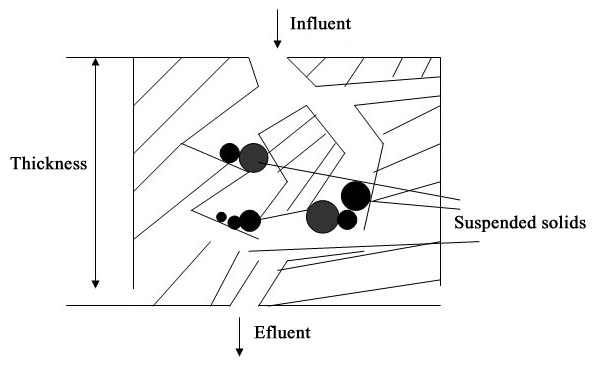
Fig. 2 Deep
bed filter with flowing channels.
4. ECOFILT Mikrofilteraa
aaThis filter construction is adapted to
existing technologies in gas production, transport and
storage. Its application allows a
simple way of requested level of gas separation and
purification. Pipeline solids, corrision products,
compressor oil, oil droplets
and oil fog can be filtered with Ecofilt Mikrofilter. By applying adequate
technology, liquid phase and mechanical impurities
can be separated from associated gas.
aaFiltering purity is 5 to 2 µm; filtering
accuracy is 95-98%; filter flow and pressure are
significant. Average initial resistance of
filter group is 0.1 bar.
aaThere is a significant advantage of Ecofilt Mikrofilter when compared to other
filters, and that is its operating lifetime of 10
years. In effect, this would mean that after cleaning,
this filter is not wasted, but returned to the system,
which, as a result,
minimizes maintenance costs. The user can plan the
maintenance cycles in advance, which makes it an input to
the system design.
Another advatage of Ecofilt Mikrofilter is that it can be installed
into existing systems to replace the existing filters,
and can even
be installed into existing housings.
aaA unique statement of our business
partners that have been using Ecofilt Mikrofilter is that it allows them to
achieve lower
costs of compressor repairs and significantly reduce
presence of impurities in the systems; Ecofilt Mikrofilter also allows for
better protection of test wells and layers. Its use can
also reduce overwork labour costs and chermical treatment
of wells.
4.1
Candle shaped filters - introduction
aaCandle shaped filters are widely used.
Its main advantage is easy installation, and another is a
relatively large filtering area on
a relatively small surface.
aaCandle or cylinder shaped filter core
serves as a base for spreading filter net - metal,
plastic, or cotton - or filter paper. The
filter core is determined by the user's design; its shape
is defined by the final goal that the user wishes to
achieve by the filtering
process.
aaThe usual candle shaped filter core is
shown in Fig. 3.
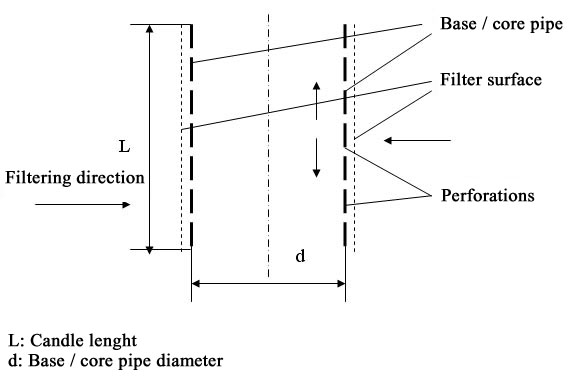
Fig. 3 Candle
shaped filter's principle
aaThe usual filter design allows for target
application and training. The L/d ratio affects the mode
of flow. Filtering quality, free
area, flitering fluid and other technical parameters have
significant effect on initial resistance, saturation time
and possibility of
cleaning.
4.2
Cascade filter
aaFilter cores can easily be rearranged in
such shapes that would allow the filtering fluid to flow
through several filtering surfaces.
The surface filter can be supplemented also with deep bed
filter. This principle allows the user to design such
filtering systems
that would result in higher level of separation and solid
suspension from the filtering fluid.
aaOne of the most important characteristics
of cascade filters is the low initial resistance. Another
advantage is high deltap value,
wich can be achieved by a robust system consruction.
aaAn important point is to have a quality
surface system that would allow filtering fluid flow for
a lengthy period of time, which
would lead to conditions for a longer filter life cycle
before replacement and a good chance to flush the filter.
The following
Figure shows one candle shaped filter cascade type.
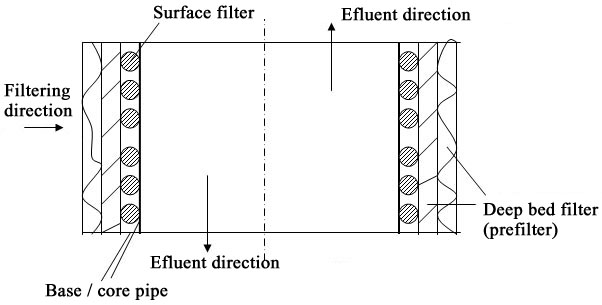
Fig. 4 Cascade
filter (3 stairs)
aaOf course the cascades are selected
according to previously conducted lab tests and requested
filtering quality. Figure 5
shows a scheme of a practically applied two-stairs
cascade filter, one surface and one deep bed filter
(prefilter).
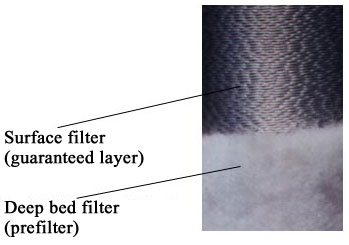
Fig. 5 Ecofilt Mikrofilter
4.3. Ecofilt
Mikrofilter
aaWhat does this trademark or name stand
for?
aaEcofilt Mikrofilter is a candle shaped cascade or
multiphase filter. As shown on Fig. 5, it is a candle
shaped filter made of
stainless steel.
aaOwing to its design, this filter is
highly resists to and allows great pressure differences
(deltap) of up to several bars.
aaFiltering surface is cylinder - candle -
shaped wrapped around the base core.
aaThe wrapping has one layer, therefore the
free surface of the filter is set with high precision
(even 98%). Thanks to the
wrapping the shape and size of the slits are also of high
precision, which is between 95-98%. This property gives
highly reliable
and precise separation of filtering surfaces.
aaMicron-gauge wire wrapped around the base
core is also made of stainless steel.
4.3.1. Based on our
experience, we can say that we have designed a robust
candle shaped filter core with low initial resistance,
which can stand great strains, and has a long operating
life of up to 10-15 years.
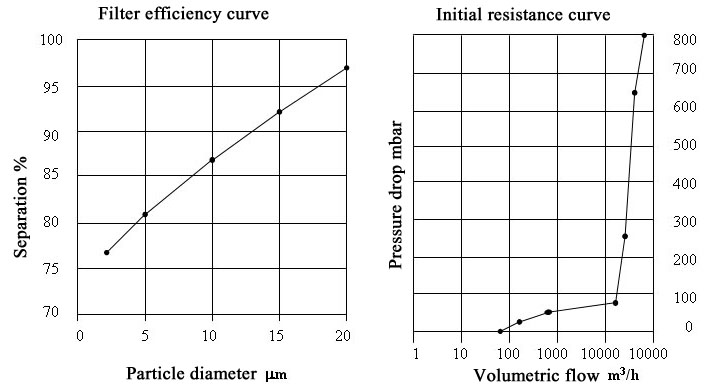
aaProduction technology in petroleum
industry allows us also to manufacture and/or alter
certain elements of the filter base core
according to the user's specific requests.
aaAs a result, it is now possible to
replace existing filter cores existing housings.
4.3.1.1 The
possibility to change the filtering parameters allows us
to maintain the existing filter surrounding. This leads
to
significant investment cost reduction.

Fig. 6
Prefilter under a microscope
aaPrefilter can be single or multilayered,
which depends on the targeted filtering process goal. By
its adequate positioning and
calibration, it can filtrate and storage large quantities
of impurity.
aaSuch filters then simplify and increase
maintenance level, since they only require replacement of
the deep bed filter.
4.3.2 Our experience has proved that the prefilters
can easily be washed (in suitable solvent); then reused,
and this
process can be repeated several times.
4.3.2.1 These
particular types of cascade filters can be applied to
industries that operate in high temperatures.
4.3.2.2 With the aEcofilt Mikrofilter such influenst, as gas,
steam, liquids, emulsion, etc. can be cleaned with
selected methods.
4.3.2.3 This filter
is highly precise, has a long operating life, gives the
user the possibility to plan its replacement, and has a
remarkable filtering efficiency to 2 µm.

Fig. 7 Filter
unit
aaCascade filters can be cleaned in a few
ways, which are very simple, unless the filtered medium
contains sticky solids.

Fig. 8 Filter
unit for gas injection into underground strorage
4.3.3 Ecofilt Mikrofilter can be supplied with
various control instruments, such as flowmeter, gauge,
velocity meter, etc.
4.3.4 All
information registered by control instruments can be
gathered into a computer data base.
aaWith the support of control instruments
there is only a step towards complete process automation.
Based on required
technical characteristics of the instruments, Ecofilt Mikrofilter allows filtering process
management from PC, by applying PLC.
aaPLC can make daily reports on filtering
process. To analyze and gather instrument information a
PLC can be upgraded
with such software that would include control, correction
and training.
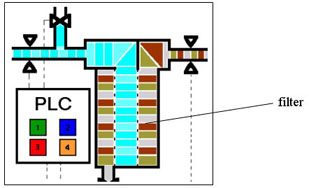
Fig. 9 PLC
4.3.5 Ecofilt Mikrofilter supported filtering unit
can be operated, controlled and cleaned using PLC
control.
4.3.5.1 All
electronic devices are adapted to the existing electronic
surrounding and processes, with which complete accord
and communication is established.
5. Summary
aaEcofilt Mikrofilter is a cascade candle shaped
filter that adapts to existing industrial processes; it
is easy to design and
calibrate, does not require high maintenance, and
eventually can be automated.
aaRobust construction of cake filter made
of stainless steel allows it to be applied to any
industrial environment where the
following is required:
- high filtering standards,
- high accuracy and precision,
- long operating cycle (long maintaining cycle that can
be planned ahead),
- safe operating in emergency situations,
- strict separation,
- long operating life,
- low maintenance costs,
- possibility of automation,
- filtration in abrasive media (gas-steam, liquid,
chemicals, etc.).
aaEcofilt Mikrofilter expands and allows the
possibility to calculate and measure mechanical
filtration without making
additional stress to the medium, and the possibility to
appley effective cleaning and flushing in both domestic
and
industrial environments to up to 2 µm. Reference of its
operation can be seen in Hungary and Serbia and
Mintenegro.
Back to the
News
|